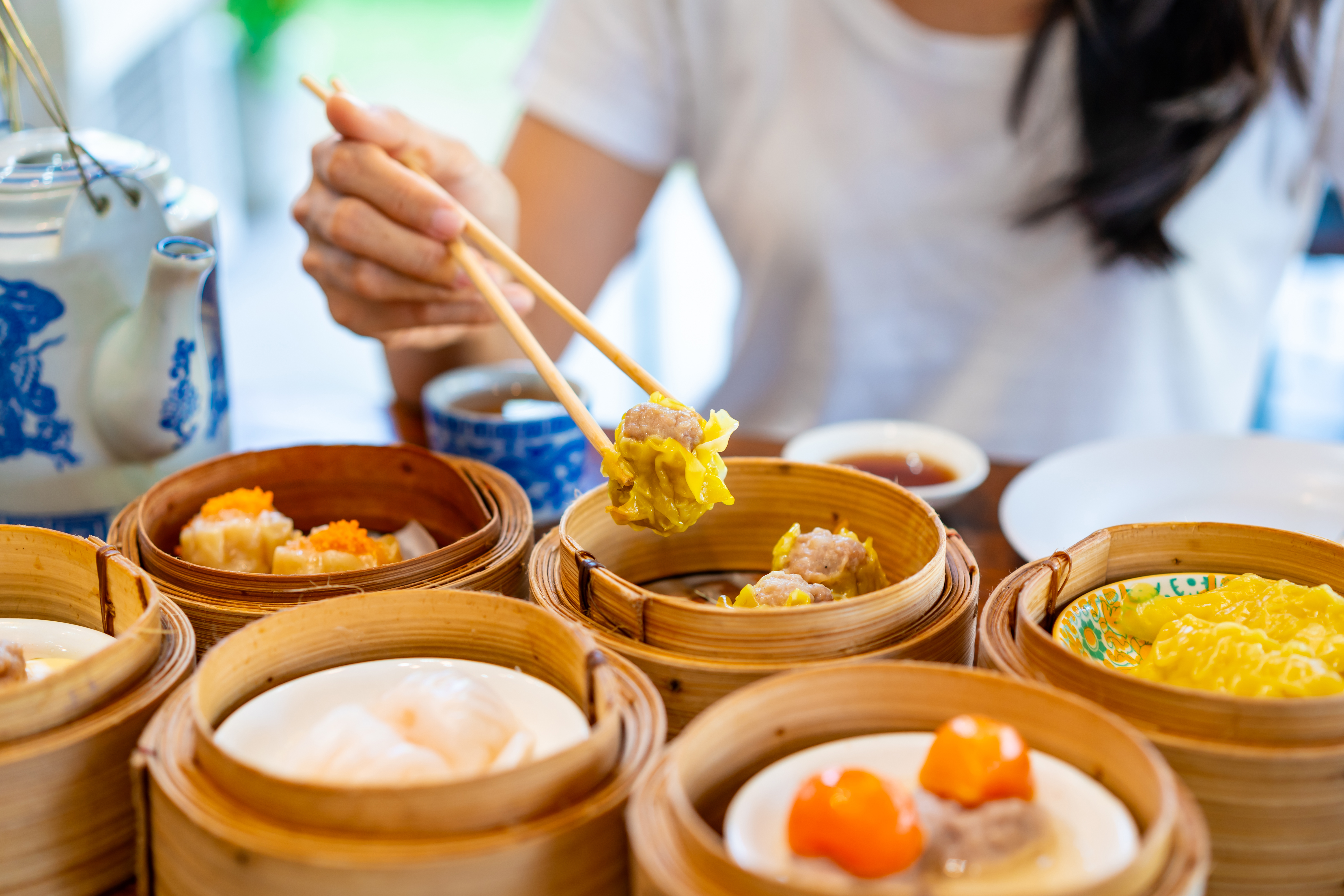
Event
Steaming Ahead: How Onboarding Solutions Help Boost Dimsum Production
Steaming Ahead: How Onboarding Solutions Help Boost Dimsum Production
Description
Singapore’s thriving food manufacturing sector
With over 1,000 enterprises comprising traditional manufacturers and food tech startups, Singapore’s thriving food manufacturing sector employed around 51,000 workers, contributed some $4 billion to our economy, and exported to more than 120 markets worldwide as of 2020.
To grow and capture more markets, our food manufacturers need to continuously innovate and improve on their productivity. However, many are Small and Medium Enterprises with limited resources to embark on job transformation and productivity initiatives.
The National Centre of Excellence for Workplace Learning at IAL (NACE@IAL), provides consultancy services to help enterprises embark on employee-driven workplace learning projects, which in turn bolster their performance. Hara Hong Kong Tim Sum is one of such enterprises who worked with NACE@IAL to boost their productivity.
A vision to be a leading Halal dimsum manufacturer
Established in 1980s, Hara is one of the few halal dimsum manufacturers in Singapore, supplying to schools, food and beverage businesses, and hotels. With a staff strength of 30, Hara has actively kept up with trends in the industry. For example, as consumers grow more health-conscious, the company uses wholemeal flour in their pau products and less sodium for specific dimsum. Today, all Hara pau and some other products are certified by Health Promotion Board as a healthier choice for food sold in school canteens.
Hara, however, faces potential operation risks amid high turnover and labour and skill shortages, which may detract it from its vision to become a leading manufacturer. To overcome the challenge, Hara worked to put in place a formal onboarding process for new hires to bring them up to speed to work in a productive manner.
Director Mr Justin Li said, “We hoped to streamline processes from the backend to production to drive the continuity of the company's mission and goals at the ground level. Through this approach, we seek to instil a sense of ownership of the importance of work safety, which is paramount to the organisation. To achieve that, staff must first know how to do the work right. The (NACE) initiative is a good starting point for the company.”
With over 1,000 enterprises comprising traditional manufacturers and food tech startups, Singapore’s thriving food manufacturing sector employed around 51,000 workers, contributed some $4 billion to our economy, and exported to more than 120 markets worldwide as of 2020.
To grow and capture more markets, our food manufacturers need to continuously innovate and improve on their productivity. However, many are Small and Medium Enterprises with limited resources to embark on job transformation and productivity initiatives.
The National Centre of Excellence for Workplace Learning at IAL (NACE@IAL), provides consultancy services to help enterprises embark on employee-driven workplace learning projects, which in turn bolster their performance. Hara Hong Kong Tim Sum is one of such enterprises who worked with NACE@IAL to boost their productivity.
A vision to be a leading Halal dimsum manufacturer
Established in 1980s, Hara is one of the few halal dimsum manufacturers in Singapore, supplying to schools, food and beverage businesses, and hotels. With a staff strength of 30, Hara has actively kept up with trends in the industry. For example, as consumers grow more health-conscious, the company uses wholemeal flour in their pau products and less sodium for specific dimsum. Today, all Hara pau and some other products are certified by Health Promotion Board as a healthier choice for food sold in school canteens.
Hara, however, faces potential operation risks amid high turnover and labour and skill shortages, which may detract it from its vision to become a leading manufacturer. To overcome the challenge, Hara worked to put in place a formal onboarding process for new hires to bring them up to speed to work in a productive manner.
Director Mr Justin Li said, “We hoped to streamline processes from the backend to production to drive the continuity of the company's mission and goals at the ground level. Through this approach, we seek to instil a sense of ownership of the importance of work safety, which is paramount to the organisation. To achieve that, staff must first know how to do the work right. The (NACE) initiative is a good starting point for the company.”
Diagnosing challenges, co-creating solutions
First step: diagnose Hara’s challenges. IAL’s consultant Ms Clare Poon went on-site to observe the work environment and production processes. Interviews were held with staff to understand work processes, scope, and pain points. Together with the company, Ms Poon guided Hara’s staff to develop the following solutions, including:
• Creation of detailed job descriptions for production workers, production supervisor, and production manager
• Created a work processes document for a specific job role in the baking department
• Developed standard procedures ranging from hiring new staff and induction to knowledge management. An onboarding checklist was created for new hires.
• Created on-the-job training guidelines
• Developed a staff handbook
Putting solutions into action
Implementation was not without challenges. One main barrier was language, as there were workers who could only speak Mandarin. To address this, English and Mandarin versions of the job descriptions and staff onboarding checklist were created. Production manager Lai Kim Wah found the checklist particularly useful, “The onboarding checklist is clear and easy to understand, especially with the pictures of processes provided. This is helpful for those who are illiterate and helps us to check if new staff can follow the processes.”
Ms Poon hoped that the handbook will make HR resources more accessible. “We observed that institutional knowledge pertaining to HR practices resided with the company’s owner and relevant administrators. We thus created a staff handbook collating all HR practices so that employees have a resource to refer to,” she shared.
A more productive dimsum manufacturer
With strong management support and the willingness of staff to share their knowledge and try new tasks, Hara successfully improved employee productivity through the project. New workers are inducted more efficiently, leading to increased production output with minimum ingredient wastage and rework.
Ms Poon also guided Hara’s senior staff to understand how to differentiate operations and job roles, and document work processes systematically. The transferred knowledge is crucial to Hara’s future workplace learning efforts. Ms Joey Loong, production manager and project champion at Hara Tim Sum, says, “This project helped us develop a systematic approach to teach the new staff with clear work processes.”
Moving forward, Hara is set to expand its workplace learning efforts to document more work processes and develop onboarding checklists for other departments.